In arc welding processes, the heat (thermal energy) required for melting the faying surfaces of the parent components are supplied by an electric arc. This arc is established between an electrode and the metallic components – both connected to a power source. The arc welding electrode can be either consumable or non-consumable. A consumable electrode melts down during welding due to the arc heating, and the molten metal subsequently deposits on the weld bead to supply filler metal. So a consumable electrode not only assists in arc formation but also acts as filler metal. On the contrary, a non-consumable electrode remains intact (does not melt) during welding. Such electrodes only assists in arc formation, and do not supply filler metal. Filler, if necessary, is required to supply externally by feeding a separate filler rod into the welding zone. Both carbon arc welding and tungsten inert gas welding are two arc welding processes that employ non-consumable electrode; however, their working principle varies widely.
Carbon Arc Welding (CAW) is a permanent joining process where coalescence is formed by melting the faying surfaces of the parent components through an electric arc established between a non-consumable carbon electrode and the components. Such carbon electrodes are made of non-graphitizing carbon black bound in a suitable semi-solid binder. The electrodes are not covered with flux (i.e. bare electrode); however, sometimes a thin copper coating is provided. The filler metal, if required, can also be supplied separately by slowly feeding a filler rod. CAW process is conventionally carried out in open atmosphere, and thus there exists high chance of chemical contamination of the hot weld metal. However, in a variant of the CAW process, called Shielded Carbon Arc Welding (S-CAW), inert shielding gas is supplied to protect the weld metal. Although the CAW electrode is non-consumable, it experiences slow disintegration with the progress of welding. Accordingly, carbon atoms from the electrode can diffuse into the molten weld metal and subsequently change the joint properties.
A sophisticated arc welding process based on non-consumable electrode is Tungsten Inert Gas (TIG) welding where the coalescence is produced by melting the faying surfaces of the parent components through an electric arc established between a non-consumable tungsten electrode and the components. Formally, TIG welding is referred to as Gas Tungsten Arc Welding (GTAW). The TIG welding electrode is made of tungsten with few alloying elements (0.2 – 1.5 %) like thorium, zirconium, lanthanum, cerium, etc. Such alloys are added for several purposes ranging from improving electron emission characteristics to reducing electrode wear rate. An inert shielding gas (argon, helium or nitrogen) is always supplied from an external gas cylinder in order to protect the hot weld metal from contamination by atmospheric air. Filler metal, if required, can also be supplied externally. If carried out properly using optimum set of parameters, TIG welding can offer defect-free reliable joints with good appearance requiring minimum effort.
Both CAW and TIG welding processes are preferably carried out under DC straight polarity (electrode negative) as it helps reducing wear rate of the non-consumable electrode. AC polarity can also be used; however, DC reverse polarity is always avoided. Whereas CAW is prone to several defects (blow holes and porosity), TIG welding can easily fetch sound joint. The extent of application of TIG welding is also vast, whereas CAW is mostly superseded by other productive and easily controllable processes. Several similarities and differences between the carbon arc welding (CAW) and tungsten inert gas (TIG) welding processes are given below in table format.
Similarity between CAW and TIG welding
- Both CAW and TIG welding are fusion welding processes as the coalescence is formed by melting the faying surfaces of the components.
- Both are arc welding processes as the heat is supplied by an electric arc formed between the electrode and the components to be joined.
- These two processes can be applied for joining electrically conductive metals only (as the parent components act as an electrode for arc formation).
- Both processes employ non-consumable electrode (it means that the electrode does not melt to supply filler metal during welding).
- In both the processes, the filler metal, if required, is supplied separately by feeding a filler rod into the welding zone.
- Autogenous welding (joining without any filler metal) of thin plates is possible with both the welding processes.
- Preferably DCSP (DCEN) polarity is used in both the welding processes. However, AC polarity can also be used in certain circumstances.
Difference between CAW and TIG welding
Carbon Arc Welding | Tungsten Inert Gas Welding |
---|---|
CAW welding electrode is made of either carbon or graphite (with copper coating). | TIG welding electrode is made of tungsten (with few alloying elements like thorium, zirconium, lanthanum, cerium, etc.). |
Electrode is relatively cheaper. | Electrode is expensive. |
Although electrode is non-consumable, electrode wear or disintegration rate is considerably high. So electrodes have shorter life. | Wear rate of the non-consumable tungsten electrode is comparatively low. So electrodes offer higher life. |
During welding, carbon particles can easily deposit on the weld bead after disintegrating from the electrode. Such additional carbon particles can easily alter the weld bead properties. | Carbon particles do not deposit on the weld bead. However, tungsten particles can get entrapped into the welded joint. |
CAW electrode has considerably larger diameter. Typically electrode diameter varies in the range of 3 – 25 mm. | TIG welding electrode has relatively smaller diameter, typically in the range of 1 – 6 mm. |
Although the electrode comes in cylindrical shape, the tip of the electrode is always made pointed (conical) to get a stable arc. Apart from conical, no other shape is used. | Although pointed-tip (conical) electrode is commonly used, various other shapes (such as truncated conical, ball tip, flat end, etc.) are also used with added benefits. |
Carbon arc welding is usually carried out in open atmosphere without the presence of shielding gas. | TIG welding is carried out in presence of an inert shielding gas (such as argon, helium, and nitrogen). |
Longer arc length (10- 30 mm) is commonly preferred for CAW. | Relatively shorter arc length (2 – 10 mm) is used in TIG welding. |
Joints are susceptible to blow holes and porosity defects. | Reliable and defect-free joints can be easily obtained if welding is carried out properly. However, chance of tungsten inclusion defect is high. |
Few varieties of carbon arc welding include (i) twin carbon arc welding, (ii) shielded carbon arc welding, and (iii) carbon arc cutting. | Some of the varieties of tungsten inert gas welding include (i) activated TIG, (ii) flux bound TIG, (iii) keyhole TIG, (iv) laser assisted TIG, (v) TIG cutting, etc. |
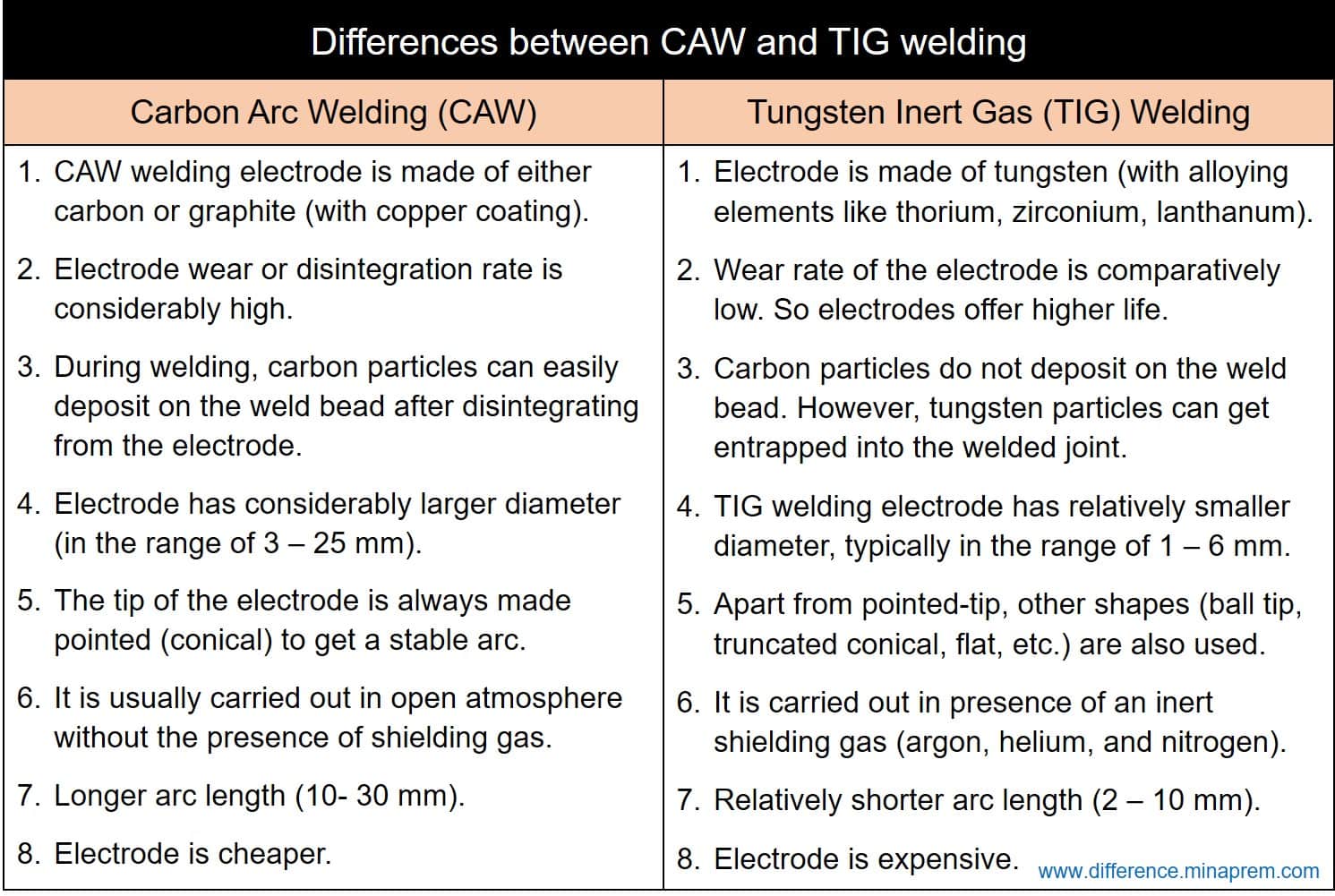
References
- Comprehensive Workshop Technology (Manufacturing Processes) by S. K. Garg (Laxmi Publications Private Limited).
- Manufacturing Technology: Foundry, Forming and Welding by P. N. Rao (Tata McGraw Hill Education Private Limited).
- A Text-Book of Welding Technology by O. P. Khanna (Dhanpat Rai Publications).