Welding is one of the manufacturing processes where two or more materials having similar or different compositions can be joined permanently with or without the external application of heat, pressure, and filler metal. In all such welding processes, where heat is applied from external source for melting the faying surfaces of the parent components, are termed as fusion welding. Arc welding processes are basically a sub-group of fusion welding processes because an electric arc supplies necessary heat for fusing the faying surfaces and filler metal. This arc is established between an electrode and the base plates; both are connected with the two terminals of a power source. Although the basic approach of joining is similar in all arc welding processes, their working principle and capability vary widely. In few processes the electrode itself supplies filler metal, whereas filler is required to supply separately in other few processes. In order to protect the molten weld metal from oxidation during the welding, atmospheric air is prevented to come in contact with the heated regions by creating a barrier surrounding the arc. Such barrier can be created either through shielding gas or through flux. GMAW and SAW are two arc welding processes having significantly different working principle and capability.
Gas Metal Arc Welding (GMAW) is one fusion welding process where the electric arc is established between a consumable wire electrode and the base plates. GMAW electrode is consumable, that means the electrode itself melts down and deposits on the weld bead to supply filler metal. GMAW electrode comes in the form of small diameter wire that is wound in the form of a spool. This wire electrode can be continuously fed for a significantly long duration during the welding. The electrodes are bare (no flux coating), and thus shielding gas is supplied for the protection of the weld metal. This shielding gas can be either inert gas (argon, helium, or oxygen) or a mixture of inert and active gases. Based on the type of shielding gas supplied, GMAW can be further classified as Metal Inert Gas (MIG) and Metal Active Gas (MAG). The arc and welding zone remain exposed during welding, and thus GMAW offers good visibility to the welder. However, for the same reason, extensive personal protections are always desired. Although GMAW offers relatively higher metal deposition rate, lack of penetration is one drawback of this process. Thus it is not suitable when thicker and wider gaps are to be filled by filler deposition.
Submerged Arc Welding (SAW) is also one fusion welding process based on consumable electrode. Here also a wire electrode is continuously fed into the welding zone from a spool. The electrode diameter is, however, somewhat larger than that used in GMAW. Although SAW employs a bare electrode, no shielding gas is supplied here. Instead, solid granular flux is delivered in large quantities ahead of the welding torch. During the welding, this granular flux gets melted owing to arc heating. This liquid flux then mixes with the oxides and other impurities of the molten weld metal to produce slag. The slag floats over the molten metal pool and thereby creates a barrier between the atmospheric air and hot weld bead. In fact, the entire arc and weld bead remain submerged under the thick slag layer. So the welding zone remains hidden from the welder. 100% of the supplied granular flux is usually not melted. A significant portion (40 – 70%) of the supplied flux remains unused. Such unused flux can be recovered and reused. SAW process offers very high metal deposition rate, and is particularly suitable for filling thick and wide gaps.
In GMAW, the arc forms in air column. It also remains exposed. Thus significant fraction of arc heat is wasted. On the contrary, the arc column in SAW process forms within liquid slag. As slag is denser medium compared to gas, the SAW arc is constricted. Heat loss through conduction also reduces significantly as the arc remains submerged into the slag layer and flux layer. These two factors together increase heat density of the arc that ultimately results in higher filler (electrode) deposition rate. While GMAW inherently produces weld spatter, SAW is free from spatter formation. Such spatter not only causes loss of filler metal but also hampers appearance, destabilizes arc, and increases injury risk to the welder. Despite having multiple benefits, SAW process is not preferred for small to medium size works. SAW process is also associated with the risk of slag entrapment defect. Various similarities and differences between GMAW and SAW are given below in table format.
Similarity between GMAW and SAW
- Both GMAW and SAW are fusion welding processes as the coalescence is produced by melting the faying surfaces of the parent component.
- Both are arc welding processes as the heat required for melting the base plates are supplied through an electric arc established between the electrode and the components that are to be joined.
- Both employ consumable electrode. Thus the electrode itself melts down due to arc heating, and subsequently deposits on the weld bead to supply filler metal. According, filler metal is not required to supply from external source.
- Both welding processes employ bare electrode. So electrodes are not coated by any flux. However, a thin copper coating is sometimes provided over the electrode to protect the metal from oxidation.
- In both the processes, electrode composition varies widely. Usually, a particular electrode composition is selected based on the compatibility with the chemical composition of the parent metals that are to be joined.
- Both processes employ continuous electrode-cum-filler. The electrode of very long length is wrapped around a cylinder to get a spool. During welding, one end of the electrode is continuously and automatically fed from this spool. Owing to very long length, a particular electrode can be fed continuously for a longer duration without interrupting the process.
- In both the processes, the arc length is adjusted automatically without any human intervention.
Difference between GMAW and SAW
GMAW | SAW |
---|---|
Shielding gas (inert or active) is supplied for the protection of the hot weld metal. No flux is required. | No shielding gas is supplied here. Instead, granular flux is supplied to shield the hot weld metal through slag formation. |
No slag formation occurs over the weld metal (as there exists no flux in this process). | The granular flux melts due to arc heat, and subsequently produces slag that floats over the weld metal. |
The arc between the electrode and workpiece is surrounded by a gaseous medium (shielding gas). | The arc remains surrounded by a liquid medium (molten flux). Such denser medium helps constricting the arc. |
Arc intensity and heat density are relatively lower. This is because – (i) the arc remains exposed, so there is more heat loss, and (ii) the arc is less constrict as it forms in air column. | Arc intensity and heat density are comparatively higher in SAW owing to constricted and submerged arc. |
Gases supplied for shielding in GMAW are vented out of the room to mix with atmospheric air. No part of supplied shielding gas can be recovered. | A part of the granular flux remains intact. The unused flux can be recovered and reused. |
The arc remains exposed in GMAW process. | Arc as well as the welding zone remains buried under the thick layer of slag and granular flux. |
The arc and molten metal pool can be observed from outside. So it offers better visibility of the arc and welding zone during the welding. | The arc and molten pool cannot be observed from outside as these are buried under the thick layer of flux. |
Spatter formation is inherent to GMAW process. Such weld spatter causes loss of costly filler metal. | SAW process is free from spatter formation. So there is no loss of filler metal in the form of spatter. |
Filler metal deposition rate is comparatively lower in GMAW. | SAW offers high volumetric filler metal deposition rate. |
Relatively less penetration (in the order of 3.5 mm per pass) is obtained by this process. | Deeper penetration (up to 10 mm per pass) can be achieved through SAW process. |
Edge preparation is desired for joining components having thickness more than 3.5 mm. | No edge preparation is required for joining components of thickness up to 10 mm. |
It is relatively less productive and less economic, especially for joining of thicker sections. | For filling thick and wide gaps, SAW is one highly productive and economic process. |
Accessories such as gas cylinder, hose pipe, etc. are needed. | Accessories such as flux hopper, roller guides, etc. are needed. |
Personal protective equipment are strictly desired for welders. | Lesser protections are desired as the arc remains submerged and invisible, and process is also free from spatter. |
It can be applied in various welding positions, including high inclination. | It is preferred for flat horizontal position only. |
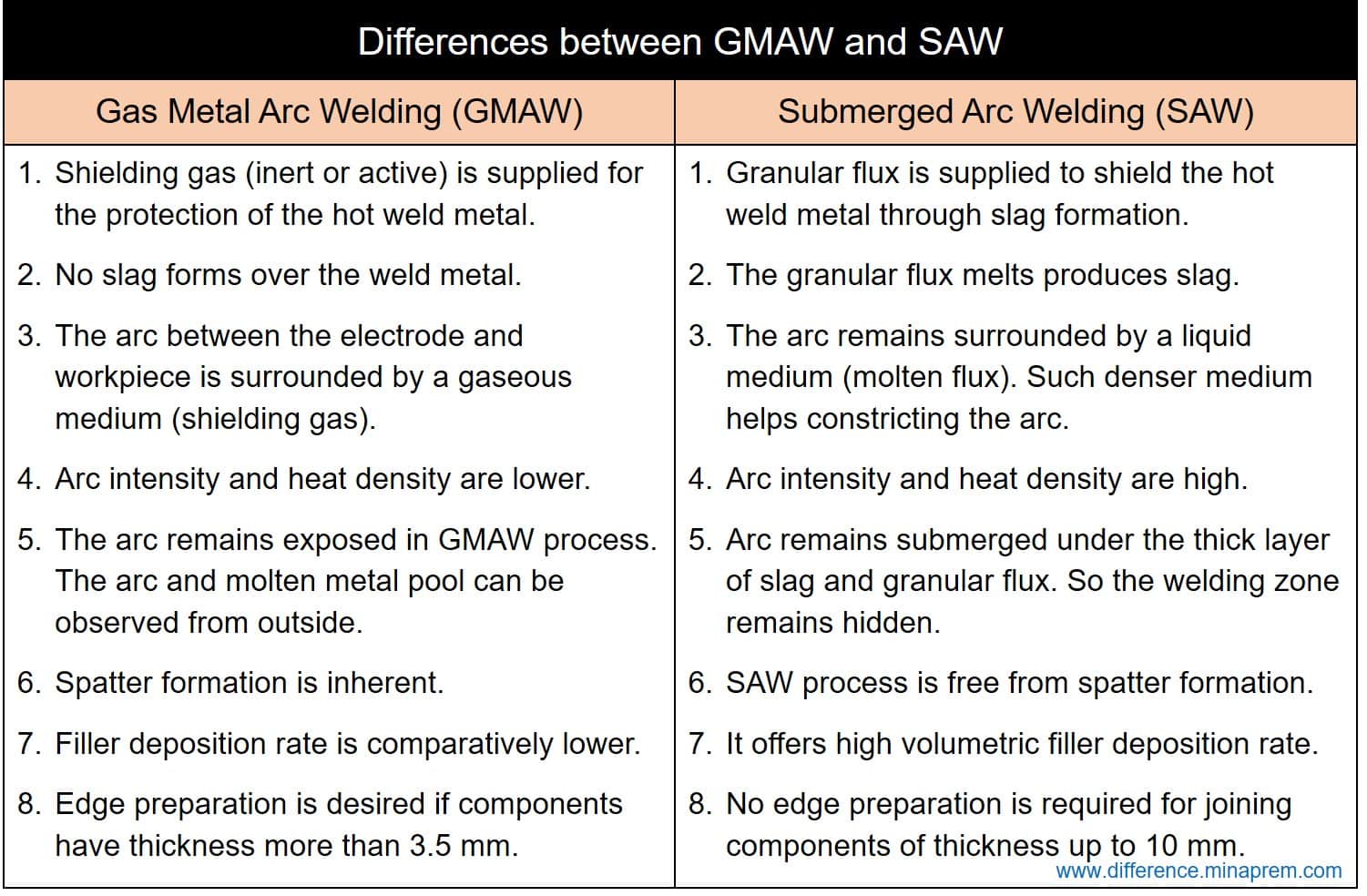
References
- A Text-Book of Welding Technology by O. P. Khanna (Dhanpat Rai Publications).
- Manufacturing Technology: Foundry, Forming and Welding by P. N. Rao (Tata McGraw Hill Education Private Limited).
- Comprehensive Workshop Technology (Manufacturing Processes) by S. K. Garg (Laxmi Publications Private Limited).