Arc welding is a sub-group of fusion welding where an electric arc is used to supply heat for fusing the parent metals for coalescence formation. The electric arc is constituted between an electrode and the base metals. The arc welding electrode can be either consumable or non-consumable. A consumable electrode is meant for melting by the arc heat, and subsequently depositing on the weld bead to supply filler metal. Such electrode assists not only in arc formation but also in filler supply. Non-consumable electrodes are, however, not meant for melting. Such electrodes do not supply filler metal; they only assist in arc formation. Regardless of electrode type, the hot weld metal is always shielded to restrict atmospheric air to come in direct contact. Such shielding can be achieved either through appropriate gas or by flux. In gas based shielding, appropriate inert gas (like Ar, He, N) or a mixture of inert and active gases (like CO2, O2) is continuously supplied surrounding the welding zone. In flux based shielding, the flux is delivered either through electrode (SMAW, FCAW) or separately (SAW). This flux disintegrates or melts to create a barrier between weld metal atmospheric air. While few welding process is carried out by gas shielding, others are based on flux shielding.
Gas Metal Arc Welding (GMAW) is one arc welding process where the electric are is established between a consumable wire electrode and the base metals. The GMAW electrode is solid wire type that is wound in the form of a spool. This electrode is continuously fed into the welding zone during welding. Since it is one consumable electrode, so the electrode itself melts and deposits on the weld bead to supply filler metal. Electrode metal composition is usually similar to that of the base metal (GMAW is preferred for homogeneous welding). The electrode is also bare (no flux coating). Accordingly, shielding is achieved through gas. Either inert gas (such as argon, helium, or nitrogen) or a mixture of inert gas and active gas (such as carbon dioxide, oxygen) can be delivered for shielding purpose. Based on the shielding gas composition, GMAW can also be classified as Metal Inert Gas (MIG) and Metal Active Gas (MAG). An active shielding gas is capable in altering weld metal properties through elemental diffusion. Although GMAW offers higher filler deposition rate, the process is capability is limited by shallow penetration and excessive spatter formation.
Flux-Cored Arc Welding (FCAW) is another arc welding process where electric arc is established between a consumable tubular electrode and the base metals. FCAW electrode is hollow in the form of a tube, where the core contains appropriate flux. Such flux contains deoxidizers, scavengers, slag formers, and other shielding agents. As the electrode melts down during welding to deposit as filler metal, the core flux also disintegrates to produce fume for gaseous shielding of the welding zone. Thus no separate supply of shielding gas is usually desired (however, occasionally shielding gas is supplied for achieving high quality joint in outdoor welding). A part of the flux also melts down and mixes with the oxides and other impurities of the molten metal to produce slag. This slag floats over the weld bead and gives an added shielding layer. However, slag also increases chance of slag entrapment defect, especially during multi-pass welding. Presence of excessive fume or smoke (gaseous product of flux disintegration) reduces the visibility of the weld zone making it difficult for overseeing the process by the human welder.
Similar to GMAW, FCAW electrode is also continuous-type having very long length, and thus it is coiled in the form of spool. This consumable electrode can be continuously fed into the welding zone for a long duration without interrupting the process. The electrode composition is mostly similar to that of the base metals. As compared to GMAW, FCAW electrode is costlier but it offers relatively deeper penetration and higher filler deposition rate per pass. However, FCAW is particularly suitable for joining ferrous metals. Both the welding processes can offer sound reliable joint requiring minimum effort. Various similarities and differences between GMAW and FCAW are given below in table format.
Similarity between GMAW and FCAW
- Both GMAW and FCAW are fusion welding processes as the faying surfaces of the base metals melt for coalescence formation.
- Both are arc welding processes as the heat required for fusing the base metals is supplied by an electric arc. This arc is constituted between an electrode and the base metals.
- Both the processes utilize consumable electrode. So the electrode melts down by arc heat, and subsequently deposits on the joint to fill the root gap.
- For both the processes, chemical composition of the electrode metal can vary widely. Suitable composition can be selected considering the compatibility with the parent metals that are to be joined.
- The electrode for both the processes is continuous type. So the length of the electrode is very long. Such long electrode is usually wound in the form of a coil or spool. No frequent replacement of the electrode is also desired.
- For both the processes, the electrode is continuously fed from the spool.
- Both the processes are carried out semi-automatically or automatically using appropriate mechanized systems.
- Autogenous welding (i.e. welding without using any filler metal) is not feasible by either of these processes as electrode-cum-filler is inherently applied.
Difference between GMAW and FCAW
GMAW | FCAW |
---|---|
GMAW employs a sloid wire-type electrode (diameter 2 – 5 mm). | FCAW employs a hollow tubular electrode (diameter 0.9 – 3.2 mm). |
Based on the volume of the filler metal, GMAW electrode is cheaper. | For same volume of filler metal, FCAW electrode is costlier. |
No flux is present within or outside the electrode. | Flux exists within the core of the tubular electrode. |
Welding zone is shielded by active or inert gas that is supplied from external cylinders. | The flux present inside the electrode disintegrates automatically during welding to provide necessary shielding. No shielding gas is supplied separately. |
Due to the absence of solid flux, slag does not form on the weld metal after the completion of welding. | Flux ingredients produce slag that floats on the molten weld bead and remains as slag coat after solidification. |
No additional step is required for the removal of the slag layer from the welded joint. | Removing the slag cover from the weld metal requires additional step. This is particularly crucial for multi-pass welding. |
The active shielding gas (such as CO2) can add or take out alloying elements into the weld metal. | Slag ingredients can add or take put chemical elements into the weld metal. |
GMAW (especially MIG) can be used for joining a wide variety of metals and alloys. | FCAW is predominantly used for joining ferrous metals. |
It offers relatively lower penetration of the weld metal. | It offers higher depth of penetration. |
Fume does not form in this process owing to the absence of flux. | Disintegration of the flux produces excessive fumes. |
Visibility is better, which is immensely helpful in maintaining the welding quality. | Owing to fume, visibility of the weld bead during welding drops, which, in turn, makes it difficult to oversee welding process by welder. |
Shielding gas supplying accessories such as gas cylinder, hose, regulators, etc. are essential for GMAW process. | Due to self-shielding, such accessories are not desired in FCAW. |
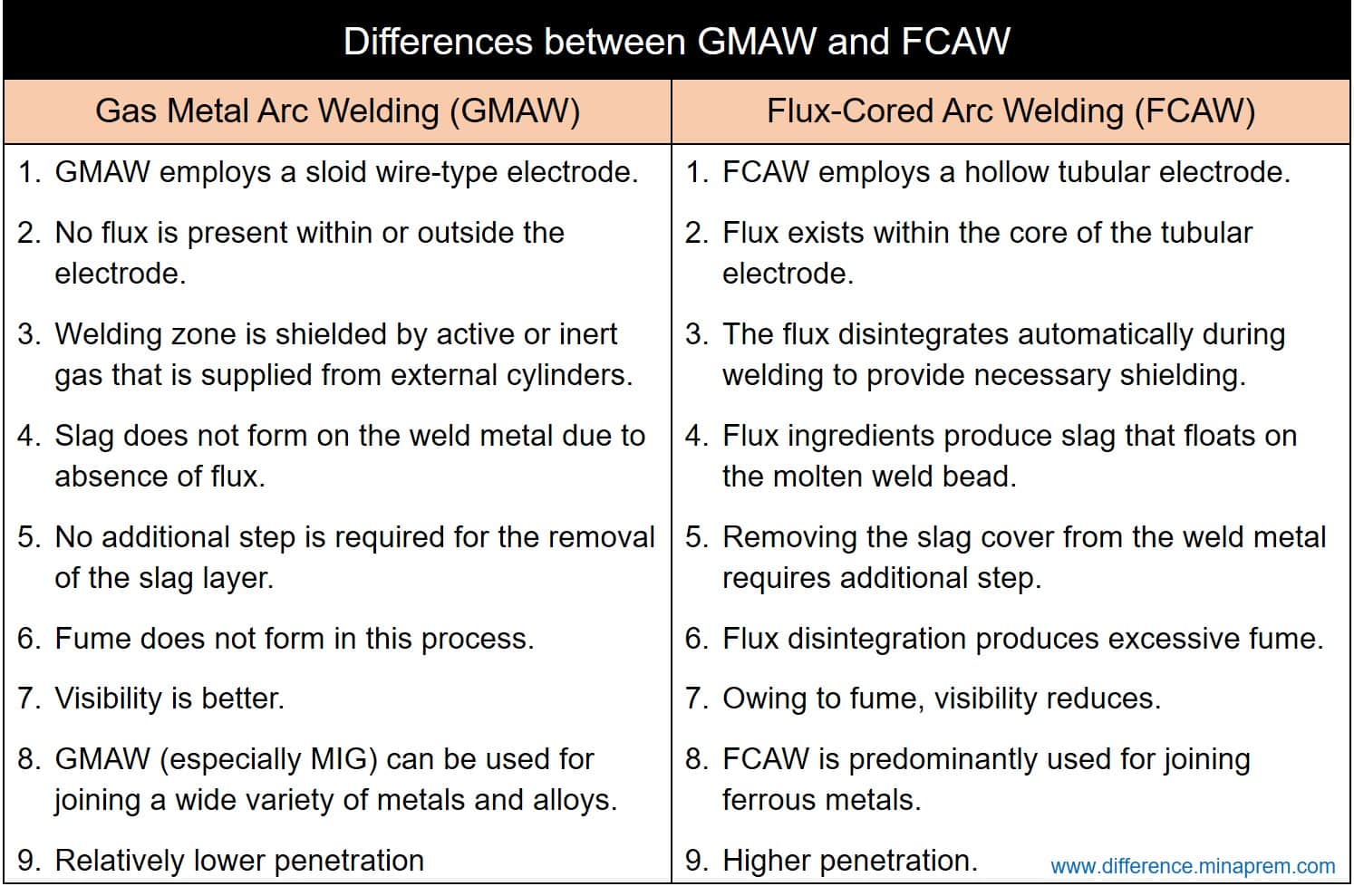
References
- A Text-Book of Welding Technology by O. P. Khanna (Dhanpat Rai Publications).
- Manufacturing Technology: Foundry, Forming and Welding by P. N. Rao (Tata McGraw Hill Education Private Limited).
- Flux Cored Arc Welding by Weldguru. https://www.weldguru.com/support-files/flux-cored-arc-welding.pdf