All arc welding processes are fusion welding; it means that the coalescence formation takes place through melting (or fusion) of the faying surfaces of the parent components. An electric arc is established between an electrode and the base plates that are to be joined. This arc supplies necessary heat for melting the faying surfaces of the base plates. The consumable electrode or the filler metal, as the case may be, also melts owing to this arc heat, and subsequently deposits on the weld bead. While the material of the weld bead is fused, material of the surrounding regions are also heated to a very high temperature (but below the melting temperature). If these molten metal and high temperature regions come in contact with atmospheric gases, then such regions can undergo various chemical reactions (particularly oxidation and reduction) that can undesirably alter welded joint properties.
To prevent direct contact of atmospheric air with the melted and heated regions of the joint, a protective layer of inert gases is usually created surrounding the arc. This thick layer of inert gas acts as a shield or barrier between the weld pool and atmospheric air during the progression of welding. There are two conventional ways of creating such barrier around the arc—either through shielding gas or through flux. In gas shielding technique, an inert gas is first retrieved from a gas cylinder and then transported to the welding torch using hose, and finally the same gas is discharged at the torch exit surrounding the electrode at a controlled flow rate. The welding torch usually have provision for controlled discharge of shielding gases.
Chemically inert gas such as argon, helium, or nitrogen (or a mixture of these gases at a predefined proportion) is usually used for shielding purpose during arc welding. Sometimes, a small percentage of an active gas (such as oxygen, carbon dioxide, etc.) is also mixed with inert gas to manipulate the properties of the weld metal through a controlled chemical reaction or elemental diffusion. Gas based shielding is relatively safer to the welder (human operator). It also offers better visibility of the weld bead, and thus it is relatively easier to weld manually when gas shielding is employed. On the other hand, flux based shielding generally produces two distinct protective layers – (i) one protective layer of gases surrounding the arc and weld bead, and (ii) another protective layer of liquid slag over the weld metal. Slag also works as purifying agent to clean the molten weld metal. The slag is basically a liquid mixture of oxides, flux ingredients, and other impurities.
Flux is a mixture of several organic and inorganic elements such as zinc chloride, ammonium chloride, calcium oxide, calcium fluoride, silicate, alumina, rutile, potassium titanate, etc. The flux can be supplied either with the electrode (flux coated or flux core) or separately as granular flux. During the arc welding, a part of the flux disintegrates to produce fumes that act as shielding gas. A part of the flux also melts and produces slag layer that protects the weld pool. Several flux ingredients also help to stabilize the arc, reduce the spatter level, enhance the viscosity of the molten metal pool, and control the weld bead properties through element diffusion. Despite its numerous benefits, flux sharply reduces the visibility of the arc owing to the fumes produced through disintegration of the flux. Thus manual welding with flux-based shielding becomes somewhat complicated. Flux shielding is also associated with the risk of slag entrapment and blow hole defects. Several similarities and differences between gas shielding and flux shielding for arc welding are given below in table format.
Similarity between shielding gas and flux for arc welding
- Both shielding gas and flux are essential elements of arc welding. While few arc welding processes utilize shielding gas, many other arc welding processes utilize flux. Arc welding without any protection is usually not recommended. Conventional carbon arc welding (CAW) is sometimes carried out without any shielding.
- Primary purposes of both these elements are same (i.e. producing an envelope of inert gases surrounding the welding zone in order to restrict uncontrolled contact between atmospheric oxygen and hot molten weld metal).
- Both can diffuse chemical elements into the weld metal. However, their capability varies widely.
Difference between shielding gas and flux for arc welding
Shielding Gas | Flux |
---|---|
Gas shielding produces only a gaseous protective layer surrounding the arc. | Flux based shielding produces both (i) gaseous protective layer surrounding the arc and (ii) liquid slag layer over the weld metal. |
No slag formation occurs over the weld metal when welding is carried out using shielding gas. | Few ingredients of flux melt and mix with oxides and other impurities to produce slag. This slag floats over the molten weld metal. |
Welding using shielding gas offers better visibility of the welding zone. | Welding using flux has poor visibility of the welding zone. |
It has low capability in altering the weld bead properties by diffusing chemical elements into the weld metal. | Flux is comparatively more efficient in altering the weld bead properties by diffusing chemical elements into the weld metal. |
It is relatively safer to the welder as it does not emit any fume. | Disintegration of flux produces flumes that are harmful to the welder. |
Respiratory protections are usually not desired if workroom windows are open. However, protections for eyes, face, skin, feet, dress, etc. are essential as usual. | Apart from other protections, welders need to wear respiratory protections (such as musk) even when workroom windows are open. |
Welding by non-consumable electrode is carried out in presence of shielding gas only. However, presence of shielding gas does not necessarily mean that the electrode is non-consumable. | Flux based welding processes always utilize consumable electrode. However, consumable electrode does not necessarily require flux. |
Autogenous welding (means that the welding is carried out without any filler metal) can be carried out with shielding gas only. | Autogenous welding cannot be carried out in presence of flux. |
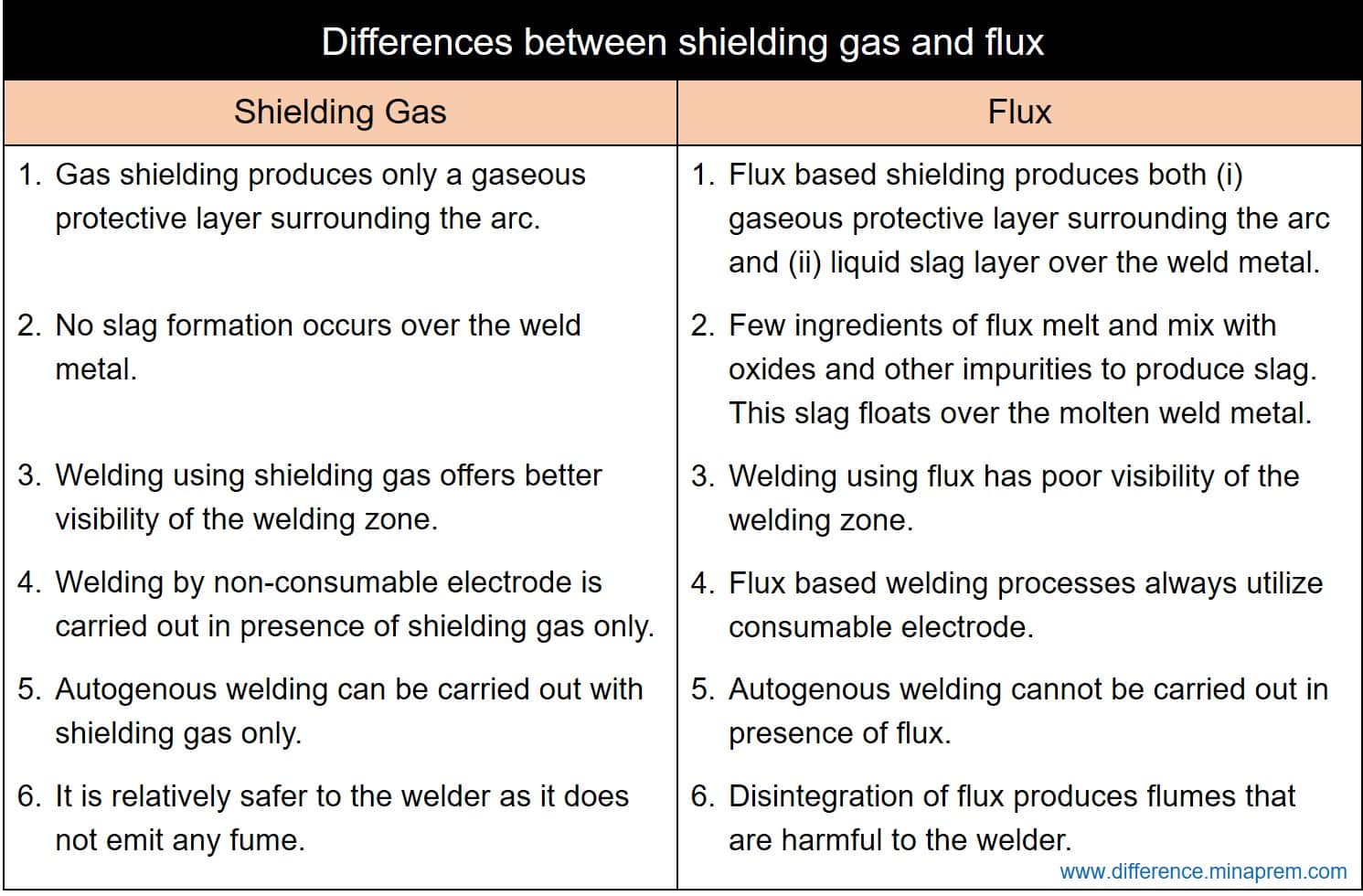
References
- A Text-Book of Welding Technology by O. P. Khanna (Dhanpat Rai Publications).
- Advanced Welding Processes by J. Norrish (Elsevier Science).