Machining is one type of subtractive manufacturing processes where excess material is removed from the workpiece to produce intended feature. Conventional machining processes (such as turning, threading, facing, milling, shaping, drilling, hobbing, etc.) employ a wedge-shaped cutting tool to shear off the workpiece material in the form of chips. Such processes always utilize mechanical energy in order to remove material by shearing. Several non-conventional machining processes have also emerged over the last few decades. Such non-traditional machining (NTM) processes can directly utilize different types of energies (such as mechanical, electrical, chemical, thermal, light, etc.) for removing materials. There are several NTM processes such as abrasive jet machining, ultrasonic machining, chemical machining, electro-chemical machining, electric discharge machining, laser beam machining, etc.
Ultrasonic Machining (USM) is one mechanical energy based NTM process which employs hard abrasive particles to remove material through the principle of “impact erosion”. A shaped-tool made of abrasion-resistant material is required, and the tool must have an inverse profile of the shape of the final intended feature. This tool is placed above the workpiece maintaining a narrow gap (25 – 40 µm). A slurry of fine-grain abrasive particles (alumina, garnet, silicon carbide, boron carbide, etc.) is continuously fed into this gap from a hopper. When low amplitude (15 – 50 µm) ultrasonic vibration (frequency > 20 kHz) is imparted on the tool, kinetic energy is transmitted into the abrasives energizing them to repeatedly strike the workpiece. When a hard abrasive particle strikes the workpiece, it erodes a tiny volume of material to produce a micron-size crater. Such repeated strikes lead to the removal of palpable volume of material.
Electric Discharge Machining (EDM) is one thermal energy based NTM process where electric spark is used to remove material through melting and vaporization. A shaped-tool is also desired in die sinking EDM, and here the tool acts as an electrode. The tool is connected with negative polarity of the power source and is placed above the workpiece maintaining a narrow gap. The workpiece is also connected with the positive terminal of the power source (thus the workpiece must be conductive). Suitable dielectric fluid (kerosene, deionized water, hydrocarbon oil, etc.) is continuously flushed in this inter-electrode gap. Normally the dielectric acts as an insulator; however, when sufficient voltage is applied across two electrodes, the dielectric breaks down creating a narrow column of conductive ions for a very short duration. A high intensity spark thus flows from the tool to the workpiece. Localized temperature at a narrow region, where the spark strikes the workpiece, increases to as high as 10,000°C. Such a high temperature can instantaneously melt and vaporize workpiece material leading to the formation of a nano-metric size cavity. Repeated generation of such sparks and consequent formation of cavities lead to palpable volume of material removal.
Although both USM and EDM are non-traditional machining processes, their principle of operation are totally different. While the mechanism of material removal in USM is impact erosion initiated by brittle fracture, the same for EDM is high temperature melting and vaporization. In USM, material is removed in solid state in the form of micro-debris. In EDM, material is removed in liquid and gaseous state (i.e. molten and vaporized form of the concerned workpiece material). Both the processes utilize a shaped tool, but the tool materials are different. However, both the processes can offer similar level of material removal rate (MRR) and surface finish. Various similarities and differences between USM and EDM are given below.
Similarity between USM and EDM
- Both USM and EDM are considered as non-traditional machining processes.
- A shaped tool (i.e. a tool having profile according to the final profile of the desired feature) is required in both the processes.
- No burr formation takes place in either of these processes.
- Both processes are independent of the chemical properties of the workpiece material.
- Both processes offer similar material removal rate (100 – 500 mm3/min).
- Both processes offer similar level of surface roughness (0.1 – 2.0 µm).
- Tapering of the side walls occurs in both the processes while cutting features having high aspect ratio.
Difference between USM and EDM
Ultrasonic Machining (USM) | Electric Discharge Machining (EDM) |
---|---|
USM is one mechanical energy based non-traditional machining process. | EDM is one thermal energy based non-traditional machining process. |
The mechanism of material removal in USM is impact erosion. | The mechanism of material removal in EDM is high temperature melting and vaporization. |
Material is removed in solid state in the form of micro-debris. | Material is removed in molten and gaseous form. |
No electrical connection is made with the workpiece. Thus workpiece is not a part of any electric circuit. In fact, no such circuit exists in USM. | The workpiece is made one electrode. It is connected with the positive terminal of the power source to receive electrons of the spark. |
This process can be applied to any workpiece material regardless of its electrical properties. | This process can be applied to electrically conductive materials only. |
The tool is made of ductile but toughened abrasion-resistant material such as steel. | The tool electrode can be made of high conductive metals, metallic alloys, non-metallic materials, or even metal and non-metal alloys (like copper, brass, tungsten, graphite, etc.). |
An abrasive slurry (abrasive particles suspended in a liquid medium) is allowed to flow through the narrow gap between the shaped tool and the workpiece. | A suitable dielectric fluid is circulated in the narrow gap between the shaped electrode and workpiece. |
USM process capability and performance depend greatly on the mechanical properties of the workpiece material (such as ductility, strength, hardness, etc.). | EDM process performance is not influenced by the mechanical properties of the workpiece material. |
No heat generation takes place in USM process. Workpiece temperature rise is usually limited to 20 – 30°C; that usually confines to a thin surface layer. | Owing to intense and repeated electric spark formation, significant heat is generated locally in EDM process. The localized temperature on the workpiece surface may even exceed 10,000°C. Note that bulk heating does not occur in EDM. |
Machined surfaces are free from thermal damages as significant temperature change does not occur during USM process. | A thin thermally damaged layer exists on the machined surface owing to very high localized temperature rise cased by the striking of spark. |
A thin layer of machined surface experiences mechanical damage as the abrasives repeatedly strike such surfaces during machining. Pertinent damages include grain deformation, residual stress inbuilt, etc.). | Machined surfaces are free from mechanical damages as these exists no solid-to-solid physical contact during machining. |
Re-cast layer (i.e. re-solidification of molten metal) does not form on the machined surface. | Incomplete vaporization and improper flushing increase the chance of re-cast layer formation on the machined surface. |
Process is associated with the risk of abrasive embedment on the finished surface, especially when the workpiece is ductile. USM is particularly suitable for brittle and non-metallic materials. | No scope of abrasive embedment in EDM process. |
It has no fire hazard as such. | Associated with risk of fire hazard owing to the presence of combustible dielectric. |
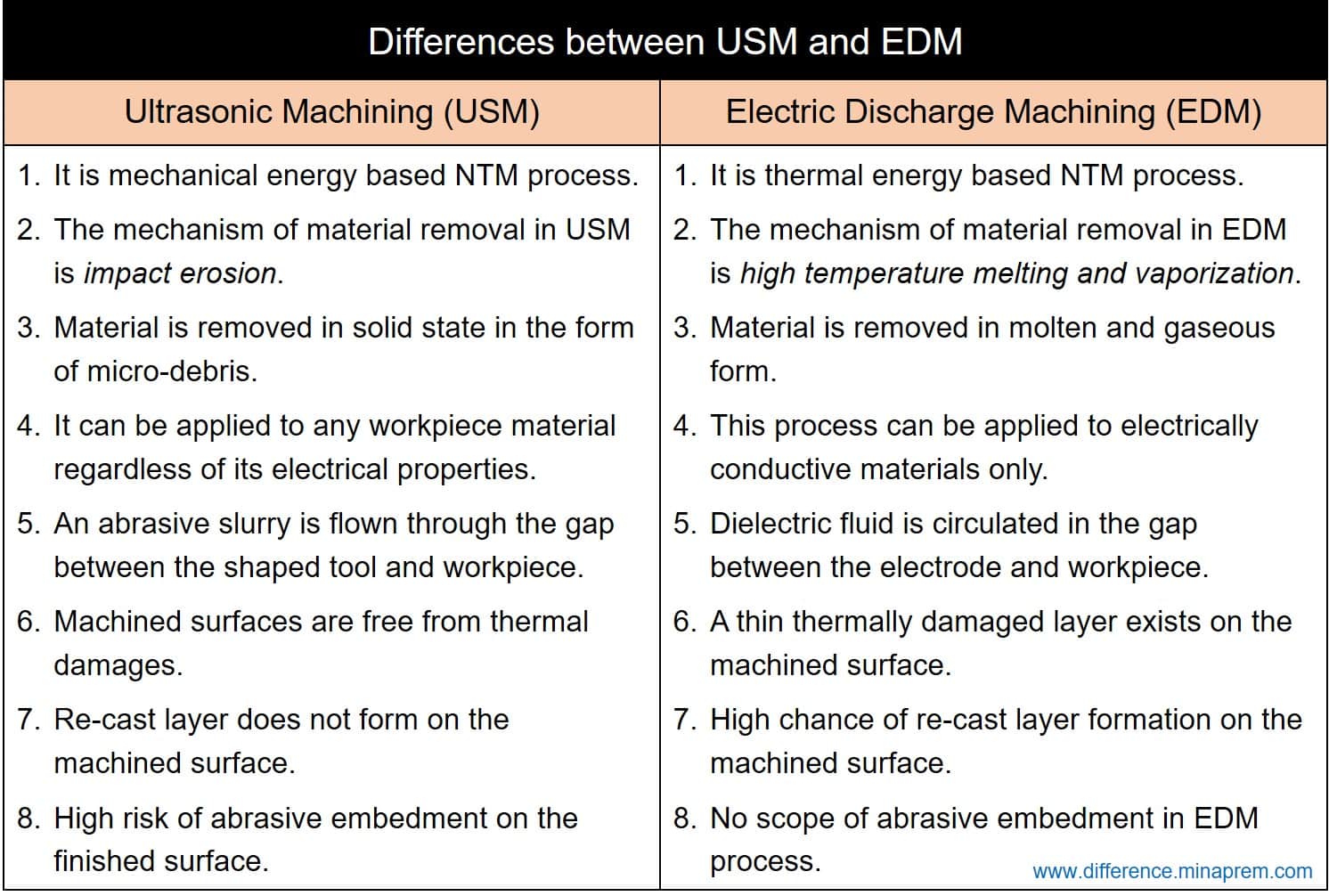
References
- Unconventional Machining Processes by T. Jagadeesha (I. K. International Publishing House Pvt. Ltd.).
- Advanced Machining Processes by V. K. Jain (Allied Publishers Private Limited).
- Nonconventional Machining by P. K. Mishra (Narosa Publishing House).