Arc welding is one class of fusion welding where the faying surfaces of the base metals are melted by supplying heat through an electric arc. The arc is constituted between an electrode and the base metals. Arc welding electrodes can be broadly classified as consumable and non-consumable. While few arc welding processes utilize consumable electrode, others employ non-consumable electrode. Consumable electrodes are meant for melting during the welding to supply filler metal. Such electrodes serve two purposes simultaneously – (i) assisting in the formation of arc, and (ii) supplying filler metal into the joint. Accordingly, no separate supply of filler metal is required. Consumable electrodes are usually made of metals having relatively lower melting temperature, and their chemical composition mostly remains similar to that of base plates. On the contrary, non-consumable electrodes are not meant for melting during welding. They remain intact, and only assist in arc formation. They do not supply filler metal. Accordingly, filler metal is required to supply separately during welding.
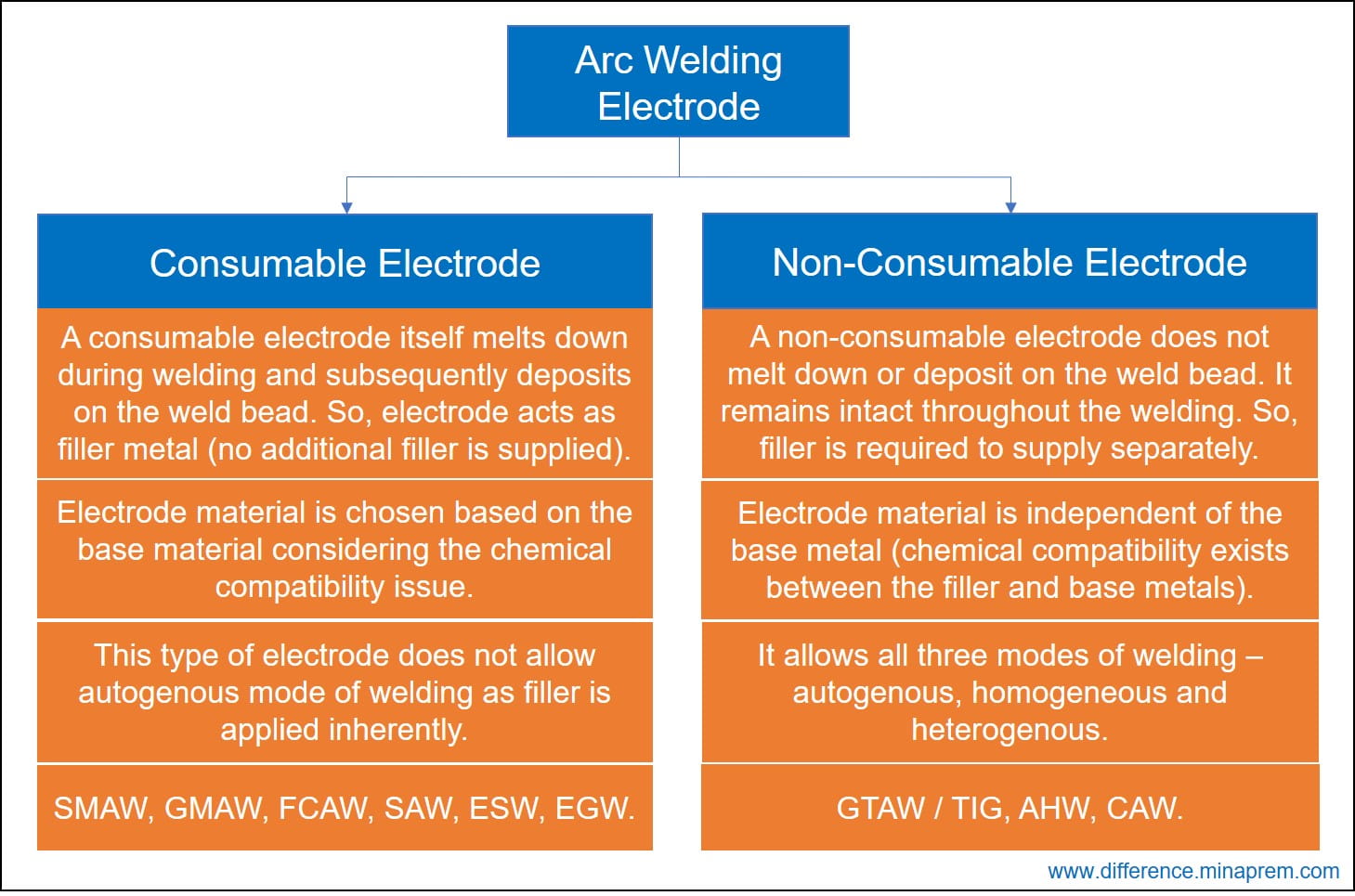
Non-consumable electrodes are made of metallic or non-metallic materials irrespective of the composition of the base metals. Carbon, graphite, and tungsten are three materials suitable for the usage as arc welding electrode (as they offer high melting point and high electrical conductivity). Carbon electrodes are made of non-graphitizing carbon black bound in a suitable semi-solid binder. These are non-metallic electrodes that offer relatively higher sublimation point. Carbon electrodes are usually coated by a thin copper coating; however, no flux coating is deposited over such electrodes. Accordingly, shielding gas is required to supply to obtain stable arc and defect-free joint. Some of the arc welding processes that employ carbon electrode include carbon arc welding (CAW) and its variants like twin carbon arc welding (T-CAW), shielded carbon arc welding (S-CAW), carbon cutting, etc.
Tungsten electrodes are also non-consumable electrodes that are made of tungsten (with few alloying elements like thorium, zirconium, lanthanum, cerium, etc.). These are metallic electrodes and offer relatively lower melting point as compared to carbon electrode. These electrodes are used in several arc welding processes, namely (i) tungsten inert gas (TIG) welding and its variants like activated TIG, keyhole TIG, etc., (ii) atomic hydrogen welding (AHW), (iii) arc spot welding, etc. Tungsten electrodes are always bare electrodes (i.e. no flux is coated on such electrodes). Usually no separate coating is also provided over such electrodes owing to chemical inertness of tungsten.
Both carbon and tungsten electrodes preferably use DC straight polarity in order to reduce electrode wear rate. Although carbon electrodes are cheaper, they come up with an inherent risk of elemental carbon diffusion into the weld bead during high temperature welding. Carbon diffusion can alter the joint properties (sometimes advantageously, sometimes disadvantageously). Such risk is not present with tungsten electrode; however, tungsten inclusion defect can happen. Carbon electrodes have several other disadvantages, such as poor form retention capability, high wear rate, susceptibility of breakage during handing and storage, etc. Several similarities and differences between carbon electrode and tungsten electrode (for the usage in arc welding) are given below in table format.
Similarity between carbon electrode and tungsten electrode
- Both carbon and tungsten electrodes are non-consumable. So these electrodes are not meant for melting and depositing during welding.
- These electrodes do not act as filler. Thus, filler metal is required to supply separately, if required.
- Both the electrodes experience slow wear with the progression of welding.
- Both these electrodes have high melting point.
- DC straight polarity (DCSP, electrode negative) is preferred during welding for these two electrodes. AC can also be applied, but DC reverse polarity (DCRP, electrode positive) is never recommended.
Difference between carbon electrode and tungsten electrode
Carbon Electrode | Tungsten Electrode |
---|---|
Carbon electrodes are made of non-graphitizing carbon black bound in a suitable semi-solid binder. | Tungsten electrodes are made of tungsten (with few alloying elements like thorium, zirconium, lanthanum, cerium, etc.). |
These are non-metallic. | These are metallic. |
Being a brittle material, it is very difficult to precisely shape the carbon electrodes. | Relatively easy to carefully shape the tungsten electrodes. |
It offers higher working temperature because of its higher sublimation point (about 6500°F or 3600°C). | It has slightly lower melting point (about 3422°C or 6192°F). |
Carbon electrodes are mostly covered by a thin coper coating layer. | No such coating is usually applied on tungsten electrodes. |
It is used in carbon arc welding (CAW) and its variants such as twin carbon arc welding (T-CAW), shielded carbon arc welding (S-CAW), carbon cutting, etc. | It is used in tungsten arc welding (TIG), atomic hydrogen welding (AHW), arc spot welding, etc. |
Carbon electrodes usually have larger diameter (3 – 25 mm). | Tungsten electrodes have relatively smaller diameter (1 – 6 mm). |
Owing to its larger diameter, the cross-sectional area of the arc is also larger. This tends to undesirably increase the widths of the weld bead and heat affected zone (HAZ). | A narrow constricted arc can be obtained with tungsten electrode owing to its better form-retention capability. This helps reducing widths of the weld bead and HAZ. |
Although theses electrodes are non-consumable, the electrode wear rate (sublimation and oxidation) is relatively high. Such electrodes have shorter service life. | Electrode wear rate of these non-consumable electrodes are comparatively lower. So tungsten electrodes offer longer service life. |
Carbon electrodes are cheaper. | Tungsten electrodes are expensive. |
These electrodes increase the risk of elemental carbon diffusion into the weld metal. Such diffusion can alter mechanical properties of the weld bead. | No chance of carbon diffusion. However, tungsten can deposit and get entrapped into the weld bead leading to tungsten inclusion defect. |
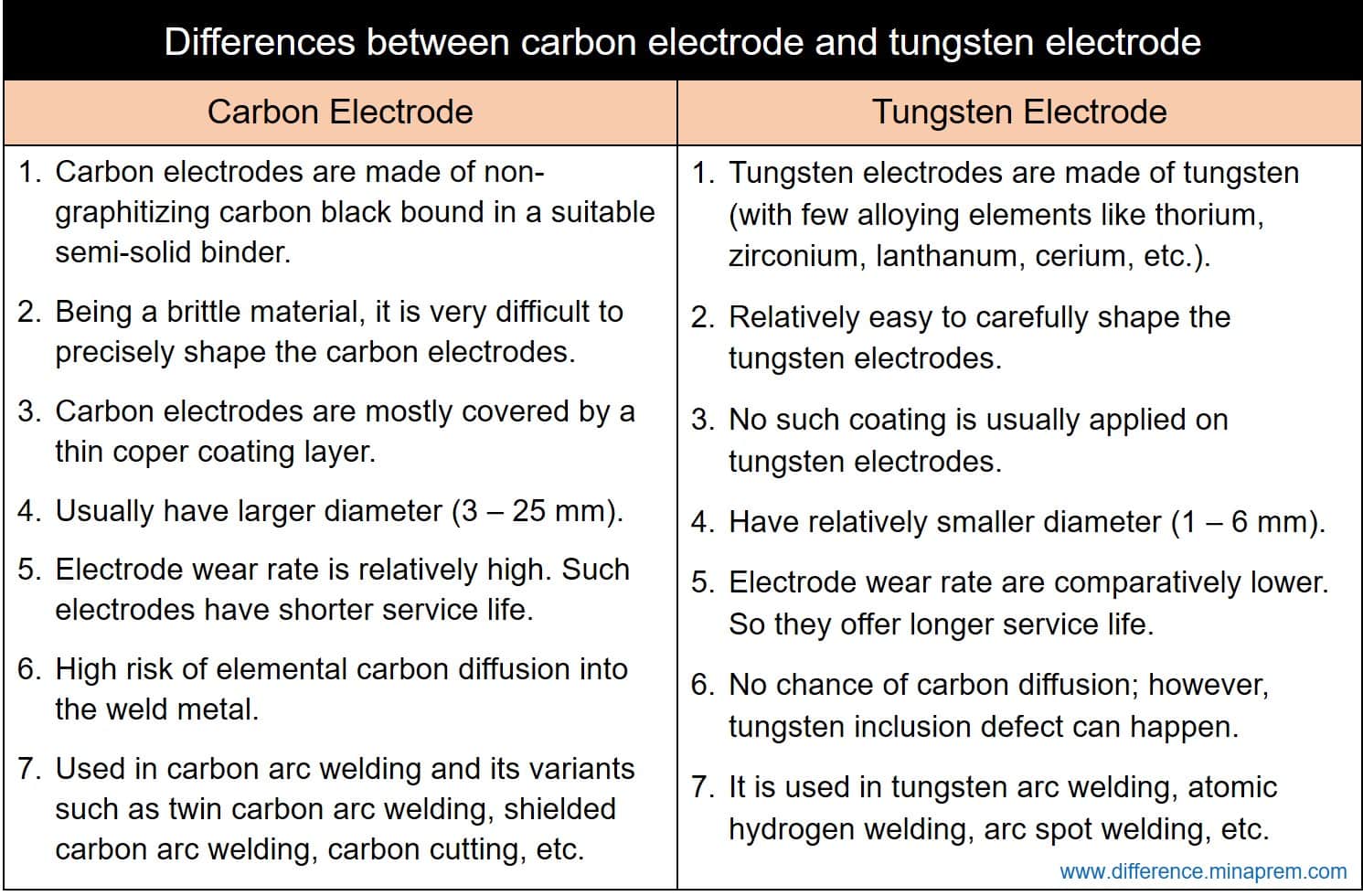
References
- A Text-Book of Welding Technology by O. P. Khanna (Dhanpat Rai Publications).
- Study Guide and Exercises for Welding Processes and Power Sources by E. R. Pierre (Burgess).