Thermal plasma is the ionic form of matter that is obtained by heating suitable gas to a very high temperature. Plasma consists of excited ions of gaseous atoms and free electrons (thus plasma can conduct electricity). Localized temperature of plasma can reach 30,000°C or even more. Such a high temperature can virtually melt and vaporize any material regardless of its physical state. An artificially created controllable jet of high temperature plasma can be utilized for several purposes including cutting or machining, welding, coating, heat treating, etc. All these processes utilize the heat of the plasma jet in different ways to fulfill the intended purpose. However, the basic requirement for such activity is a constricted jet of high temperature plasma flowing at high velocity. In order to artificially generate plasma, a plasma-forming gas (can be air, hydrogen, argon, or nitrogen) is introduced into a gas chamber at a high flow rate (1 – 5 m3/h). The gas chamber contains a tungsten electrode, which is connected with the negative terminal (cathode) of a DC power source. The positive terminal of the power source can be connected either with workpiece or with the nozzle of the gas chamber. Based on this connection, plasma torch (plasmatron) can be classified as transferred arc plasma torch and non-transferred arc plasma torch.
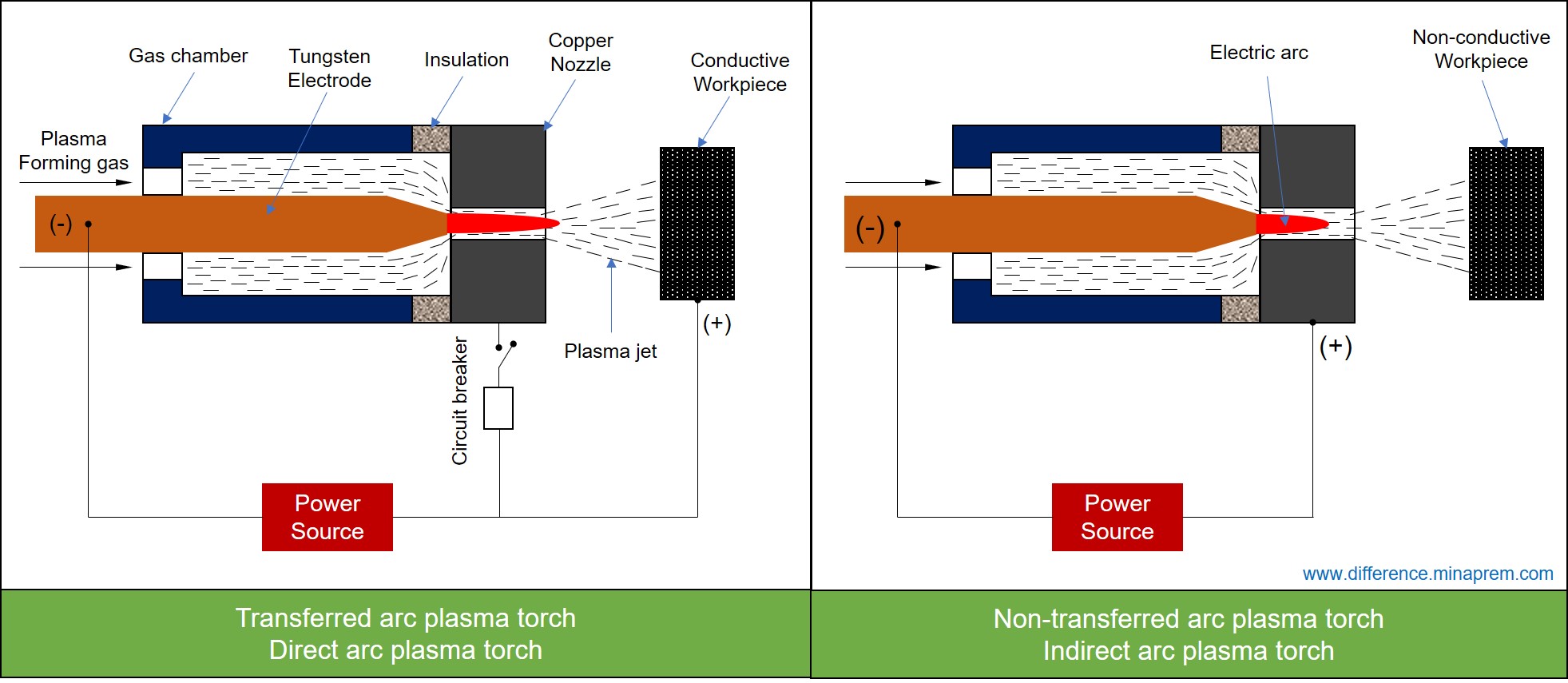
In transferred arc plasma torch, the workpiece is made an integral part of the electrical circuit. Therefore, the positive terminal of the DC power source is connected to the workpiece (while the electrode remains connected with the negative terminal). No need to mention that the workpiece must be electrically conductive. When sufficient voltage (around 200 V) is applied across two terminals, a long electrical arc forms between the electrode and workpiece through the small nozzle opening. As it is difficult to establish the arc directly between the electrode and workpiece (because of 5 – 10 mm gap), an auxiliary arc is established between the electrode and nozzle at the beginning of the work for a very short period. The plasma-forming gas that is pumped into the gas-chamber comes out through the small nozzle opening surrounding the electric arc. Owing to the high arc temperature, the gas automatically gets converted to plasma and emerges out of the nozzle in the form of a jet to finally strike the workpiece. The transferred arc plasma torch is also known as direct arc plasma torch as electrical connection is made directly between the electrode and workpiece. The problem with this arrangement arises when the workpiece is not electrically conductive. In such cases, the copper nozzle is connected to the positive terminal (anode) of the DC power source, while no connection is made with the workpiece. Such an arrangement is known as non-transferred arc plasma torch or indirect arc plasma torch. Here electric arc forms between the electrode and the nozzle. However, the plasma-forming gas forcefully directs the arc into the small nozzle opening, while itself gets converted to plasma and comes out of the nozzle as a high temperature high velocity jet. Various similarities and differences between transferred and non-transferred plasma torch are given below in table format.
Similarities between transferred and non-transferred arc plasma torch
- In both the cases, an electrode is indispensably used to liberate electrons. This electrode is given negative polarity (cathode).
- Both the arc systems are based on DC (direct current). The voltage remains around 200 V, while current can be as high as 1,000 A.
- Plasma forming gas (like air, hydrogen, argon, or nitrogen) is also required to pump into the gas chamber continuously regardless of the type of plasma torch used.
- In both the cases, an electric arc supplies necessary heat to form plasma.
- Irrespective of the torch type, plasma beam operations are very noisy. Accordingly, proper personal protection must be used while operating plasma machines.
Differences between transferred and non-transferred arc plasma torch
Transferred Arc Plasma Torch | Non-transferred Arc Plasma Torch |
---|---|
The electric arc is constituted between an electrode and the workpiece. However, an auxiliary arc is established between the electrode and nozzle at the beginning of the work for a very short period. | The electric arc is constituted between an electrode and the nozzle, and the same arc is continued for the entire operation. |
Here the workpiece is made anode (positive terminal of DC power source), whereas the nozzle is kept electrically neutral. Cathode is always a copper electrode. | Here the workpiece is kept electrically neutral, whereas nozzle is made anode. As usual, cathode is always a copper electrode. |
Direct arc plasma torch can be applied to electrically conductive workpieces only. | Indirect arc plasma torch can be applied to every workpiece regardless of electrical conductivity. However, it is preferred for non-conducting materials. |
Direct arc has relatively higher electro-thermal efficiency (85 – 95%). | Indirect arc has comparatively low electro-thermal efficiency (65 – 75%). |
Direct arc is overwhelmingly used for machining (or cutting), welding, hardfacing, remelting, and spraying. | Indirect arc is preferred for flame spraying, spheroidizing heat treatment, ore processing, etc. |
Transferred arc plasma torch is also known as “Direct Arc Plasma Torch” because the arc is maintained directly between the electrode and workpiece. | Non-transferred arc plasma torch is also known as “Indirect Arc Plasma Torch” because the arc is not maintained between the electrode and workpiece though the workpiece receives the heat. |
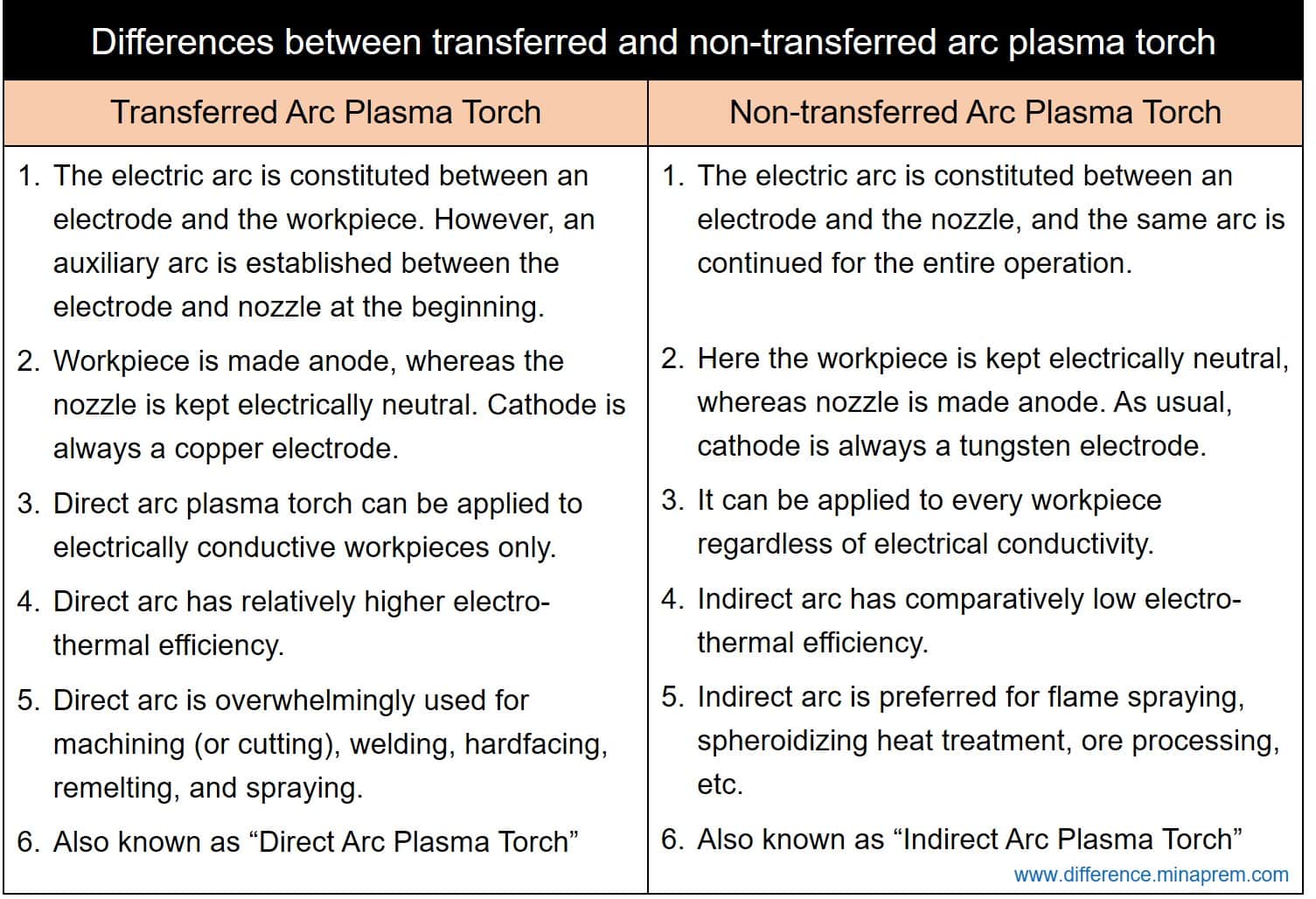
References
- Modern Arc Welding Technology by Ador Welding Limited (Oxford and IBH Publishing Company Pvt. Ltd.).
- Nonconventional Machining by P. K. Mishra (Narosa Publishing House).